Solder Seal Wire Connector
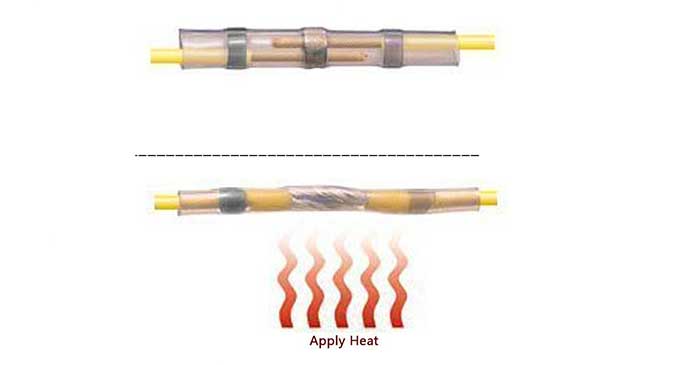
Soldering without a soldering iron
What if you had a means of connecting (in-line) a wide variety of wires types which was:
1. fairly convenient
2. works on solid or twisted core or combo of each
3. relatively inexpensive (as low as $.13 each)
4. very reliable
5. virtually waterproof (with colored glue rings)
6. as strong as the original wire
7. small, doesn’t add much bulk to the wire
8. no special tools needed to complete the connection
9. makes a totally visible connection
10. involves soldering, but no soldering iron!
11. doesn’t involve any crimping
12. not “greasy” and doesn’t leak anything
Well, it does exist, and it’s called a Solder Seal Wire Connector This connector offers all of the key characteristics listed above. I don’t think there’s any other connector that can do what this one does. Items #9 and #10 are especially important for ensuring great, long-term connections. In addition to its shrink-nature, it uses a small ring of “low” temperature solder (with flux) which you can witness flowing all around the two wires. This is its key “wow” feature. You need a source of heat but this is easily obtained with a lighter or match or small heat gun. The only downside is you still have to strip the wire. It does take a bit of practice but once you get the hang of it, it’s pretty neat.
Basically, with one step you get a soldered, sealed, and insulated connection. It’s not as convenient as Scotchlok (or other) butt connectors, but those only work (reliably) with solid-core wire. Plus those are bulky and not in-line connections, nor are they as strong.
Here are all the steps:
1. strip both ends of the wires you want to connect
2. add a properly sized connector down one side (much like you would add some heat-shrink tubing)
3. twist the exposed wires together, in-line (optional)
4. move and orient the connector around the joint making sure the solder ring surrounds both bare wires.
5. heat it up and watch it shrink and the solder flows into the connection (it shrinks first, then the solder flows).
6. Crucially, don’t move the connection until the solder has had time to fully cool (about 30-seconds).
7. closely examine the joint to ensure the solder has fully covered both wires. This is more likely if you twist them first (step #3).
That’s it…it’s a brave, new world of wiring!
This is a Cool Tools favorite from 2017
11/3/21180pcs Solder Seal Wire Connectors